Advanced PV Technologies for Harsh MENA Solar Conditions
As utility-scale solar development expands across the Gulf and North African regions, selecting the right module technology is critical to performance, ROI, and long-term system resilience. This technical case study offers an in-depth comparison of PERC, TOPCon, HJT, and IBC panel architectures, evaluating how they withstand high heat, UV stress, sand abrasion, and albedo gain in desert climates. From temperature coefficients and degradation rates to bifaciality and PID resistance, the study equips energy professionals with the data they need to make smart technology choices in high-irradiance markets like Saudi Arabia and the UAE.
Technology Architecture Deep Dive
Detailed comparison of PERC, TOPCon, HJT, and IBC technologies for thermal stability, bifacial gain, and field degradation under MENA climate stress.
Environmental Performance Metrics
Insights on temperature coefficients, albedo optimization, UV resistance, PID mitigation, and field-tested module durability in desert deployments.
Strategic Deployment Guidance
Essential reading for EPCs, developers, and utility-scale planners seeking to optimize module selection for long-term output and investment return in harsh terrain.
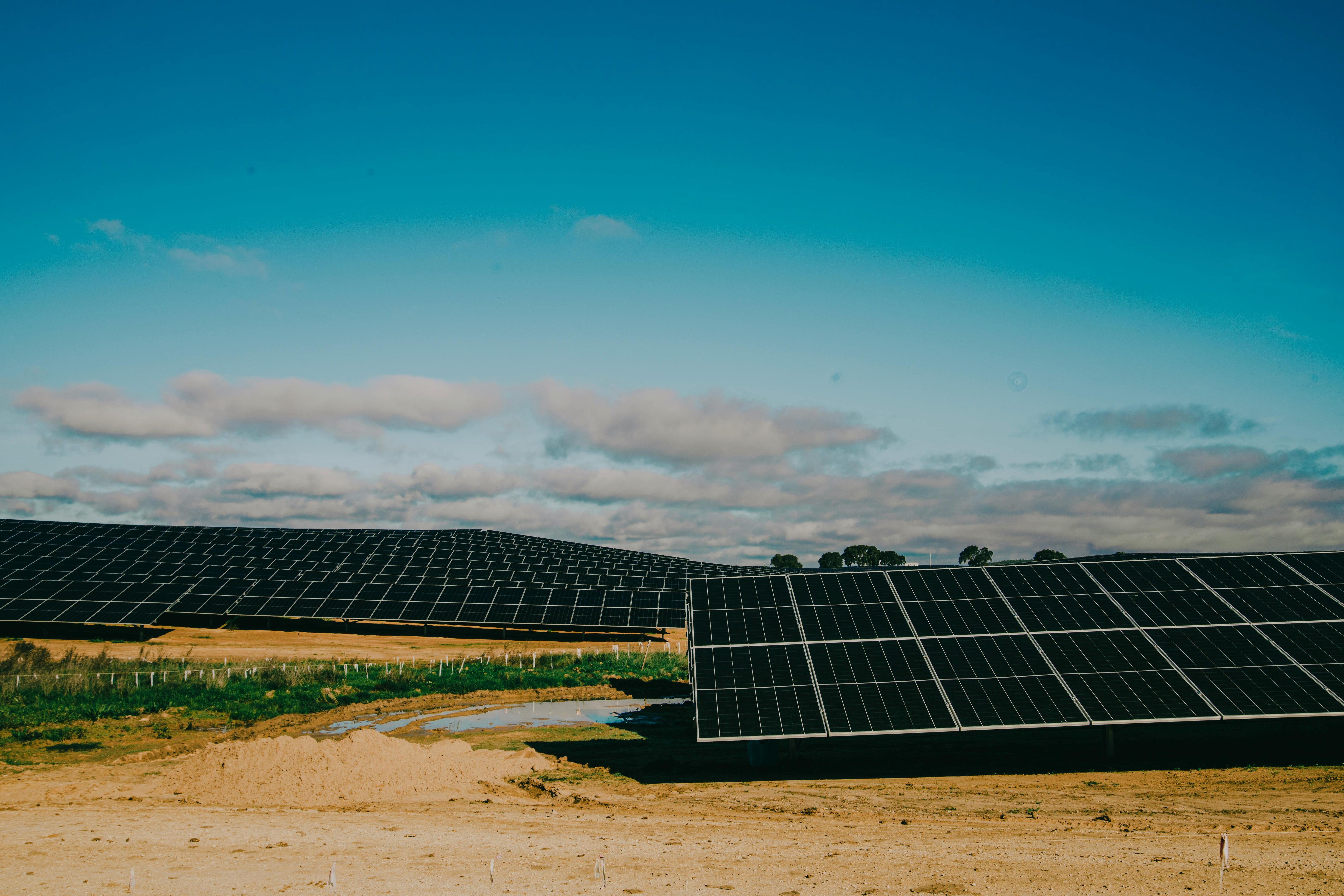
Gletscher Energy R&D Team | Energy Strategy & Infrastructure Division
Introduction
In the high‑irradiance deserts of the Middle East and North Africa (MENA), solar PV projects are shifting toward the latest high‑efficiency cell architectures to maximize yield and reliability. Today’s market is dominated by four key crystalline‑silicon technologies – p‑type PERC (Passivated Emitter Rear Cell) and three n‑type variants: TOPCon (Tunnel Oxide Passivated Contact), SHJ/HJT (Silicon Heterojunction), and IBC (Interdigitated Back Contact). Unlike legacy mono‑PERC, these next‑generation cells incorporate advanced rear-passivation or contact schemes and often double‑sided collection. Each offers distinct tradeoffs in efficiency, thermal performance, bifaciality, and degradation, which are critical under desert stress. Here we dive into the technical differences:
PERC (p-type, n+/p structure)
The incumbent technology (20–22% module efficiency) adds a dielectric rear passivation and laser‑opened contact holes on a p‑type wafer. PERC is cost‑effective and well‑established, but it is prone to light‑induced degradation (LID/LeTID) and has a relatively high temperature coefficient (~–0.35%/°C). It is typically monofacial and has a lower bifacial factor (~70% of the front side) than newer cells.
TOPCon (n-type, ultra‑thin oxide + poly‑Si)
This is essentially an n‑type PERC upgrade. A ~1–2 nm silicon oxide layer with doped polysilicon on the rear suppresses recombination, pushing record cell efficiencies into the mid‑20s% (26%+ in lab, 24%+ in production) TOPCon modules retain compatibility with existing PERC lines (modest capital upgrade) and excel in hot climates: they typically have a moderate temperature coefficient (–0.29 to –0.30%/°C) and high rear‑side sensitivity (bifaciality up to ~85%). In desert operation, TOPCon’s robust passivation and use of n‑type silicon greatly reduce LID, though emerging LeTID must be managed. One drawback is higher silver consumption than PERC, which increases cell cost.
HJT/SHJ (n-type, crystalline + amorphous silicon)
Silicon Heterojunction cells use an n‑type wafer coated with intrinsic and doped amorphous silicon layers. This “double‑junction” design yields the highest open‑circuit voltages and excellent low‑temperature coefficients (~–0.25%/°C). HJT panels have achieved ~26.6% cell efficiency in R&D and ~24%+ in volume production, with record bifacial factors (>90%). They show negligible LID and LEO‑like stability under humidity. However, HJT requires completely new manufacturing lines (indium tin oxide coatings, dual deposition) and is sensitive to process variations. Notably, recent 3‑year field data from Qatar show some HJT modules experiencing the highest degradation (~8.7% power loss over three years) among advanced modules, mainly due to encapsulant delamination under intense UV and heat. This underscores that even “ideal” cell tech must be paired with rugged module design in the desert.
IBC (n-type, all-back-contact)
IBC cells (pioneered by SunPower) eliminate front contacts by placing both positive and negative contacts on the rear. The exposed front surface is pure silicon, so the theoretical efficiency limit is ~29.1% (versus ~28.7% for TOPCon, ~27.5% for HJT). In practice, commercial IBC modules reach ~22–24% efficiency. Their inherent advantages include very low temperature coefficients (comparable to or better than HJT ) and exceptionally low degradation (often ~0.4% per year after initial stabilization). IBC modules also handle heat well due to uniform current collection on the back. The catch is manufacturing complexity: IBC cells require specialized diffusion and metallization and cannot use existing PERC lines, so capex is high. Typically, IBC is offered as premium or niche modules. Notably, PV Tech notes IBC modules exhibit improved stability compared to PERC/TOPCon/HJT under desert stress, likely due to their all-rear contact design.
Key Performance Metrics in Desert PV
Extreme desert climates (high irradiance, temperature, dust, and UV) demand special attention to performance factors:
Temperature Coefficient
Every °C above 25°C reduces output by the TC fraction. Desert peak cell temperatures often exceed 60°C, so a low magnitude TC is vital. N-type cells dominate here: e.g., TOPCon modules are typically ~–0.30%/°C (meaning ~86% of rated power retained at 45°C), whereas HJT can reach ~–0.25%/°C. By contrast, conventional p-PERC often loses ~0.35–0.40%/°C. This means HJT/IBC can generate ~5–10% more energy on hot days compared to PERC.
Irradiance and Albedo (Bifacial Gain)
Deserts have very high sun intensity and moderate ground reflectance (e.g., pale sand can reflect ~20–30% of sunlight upward). Bifacial modules can exploit this by capturing rear‑side light. State-of-the-art bifacial PV on single‑axis trackers can boost energy yield by ~40% over fixed monofacial arrays. Even fixed-tilt bifacial arrays see ~20–30% more annual output. For example, N-type TOPCon modules with 85% bifaciality (Jinko’s Tiger Neo) used in Saudi projects claim ~3.4% absolute energy gain from albedo. Optimizing the rear-side spectral response (EQE) is critical – modules should match the reflected spectrum of desert surfaces for maximum gain.
UV and Soiling
Intense UV in deserts accelerates encapsulant yellowing, backsheet chalking, and cell encapsulant delamination. Likewise, sand and dust adhesion can abrade glass coatings. Research shows soiling losses in hot deserts can be ~1% per day without cleaning. Module fronts use tempered, textured glass and durable AR/AS (anti-reflective/anti-soiling) coatings to mitigate this . Glass is preferred over polymer fronts because it sheds dust more readily. System designers often schedule daily or weekly wash cycles and use robust interconnects (e.g., SmartWire or conductive adhesives) to handle thermomechanical stress from cleaning equipment.
Potential-Induced Degradation (PID)
High system voltages under arid/dusty conditions can lead to PID, driven by ion migration. N-type cells inherently resist PID better than p-type cells. Desert-grade modules use zero-acetic polymer encapsulants (e.g., POE) and backsheets engineered for low ionic content. For instance, standards recommend encapsulants with volume resistivity ≥10^16 Ω·cm to block leakage currents, and backsheets with acetic acid transmission (AATR) <0.5–1 g/m²·day to avoid acid corrosion and PID. These measures, plus double‑glass laminates, greatly improve long-term stability.
Humidity and Corrosion
Although desert air is dry, occasional humidity (dew, monsoons) can be corrosive. Backsheets are chosen for high UV stability and multi-layer polymer stacks for insulation. Vaulted junction box designs and humidity-resistant module rails are also used.
Field Insights and Regional Deployments
Recent field trials in the Gulf deserts validate these trends.
A 3‑year comparative study in Qatar (DOI: Solar Energy, 2025) tested commercial PERC, TOPCon, and HJT modules outdoors. It found TOPCon modules had the lowest overall degradation (as little as 0.14% over three years), while HJT showed the highest (up to 8.73% loss), despite HJT’s superior specs.
Notably, bifacial HJT and TOPCon modules generated higher specific energy yields than PERC in summer. One PERC model with advanced materials even matched the advanced cells, highlighting that construction quality is crucial.
The study also quantified thermal losses: at peak heat, TOPCon lost ~9.9% of PR (performance ratio) vs only ~5% for the best HJT module, reflecting their TC differences.
Gulf projects are already leveraging advanced modules. In Saudi Arabia, Jinko has secured 1.75 GW of contracts for N-type TOPCon “Tiger Neo” modules on desert farms. These large plants (Medina and Ha’il provinces) deliberately use high-bifaciality modules (85% rear factor) to squeeze extra energy from sand albedo.
Microclimate simulations suggest that the modules’ albedo gain can reach a +3.4% net yield in flat-sand terrain, with even higher gains if white gravel or salt flats are used. This reflects a broader Gulf trend: Vision 2030 goals encourage pushing efficiency and yield, so projects favor n-type bifacial panels with superior heat tolerance.
Conclusion and Tools
Designing high-performance solar systems for the MENA region is not a matter of choosing between bifacial and monofacial modules—it requires a comprehensive understanding of how different PV technologies respond to the region’s extreme climate variables. High ambient temperatures, elevated UV levels, sand accumulation, and harsh humidity cycles can all erode system efficiency and long-term financial viability if not properly accounted for.
To build truly desert-optimized PV systems, engineers must evaluate not only front-side efficiency but also degradation behavior, temperature coefficients, PID susceptibility, and the materials science behind encapsulation and backsheet design. Technologies like HJT and IBC offer advantages in thermal resilience and long-term stability, while TOPCon balances efficiency with production scalability and strong bifacial response. PERC, though widespread, faces inherent limitations under MENA-specific stressors unless enhanced with advanced material engineering.
Furthermore, the potential of bifacial modules in MENA is only fully realized when paired with optimized ground reflectivity, mounting orientation, and cleaning strategies. System performance is shaped as much by microclimate and deployment context as by module choice.
For stakeholders making high-stakes decisions—whether at the level of procurement, plant design, or policy—relying on lab-rated specs alone is not enough. Real-world modeling and environmental simulation must guide technology selection.
At Gletscher Energy, our updated Solar Demand Calculator allows integrators, developers, and infrastructure planners to simulate performance across PV architectures—PERC, TOPCon, HJT, and IBC—based on local irradiance, heat profiles, albedo conditions, and expected operating temperatures.
Start optimizing your next solar deployment with data that reflects reality, not just theory.
-
-
-
-
-
-